ヘリカルピアの品質
Quality of Helical Pier
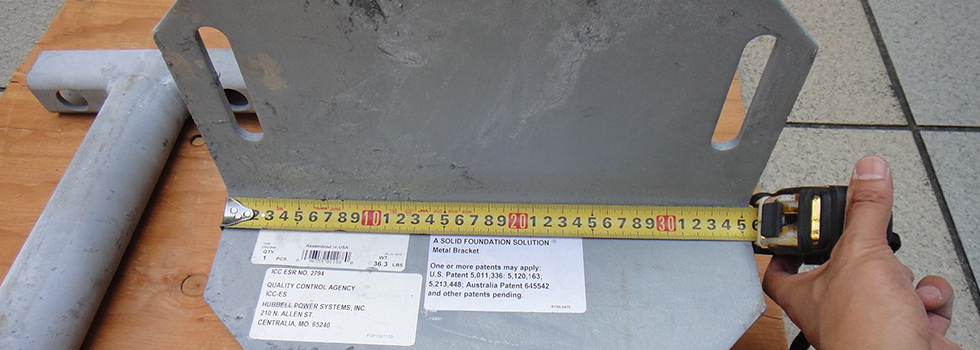
ヘリカルピアの品質
Quality of Helical Pier
ミズーリ州にあるセントラリア工場では、鋼材仕入から、パンチング、切断、鍛造、溶接、組立、メッキ加工、出荷前検査、梱包、納品までの全行程を自社で行う一貫生産ラインを構築しており、ヘリカルピアの品質を保証する大きな強みとなっています。
安定した品質
ヘリカルピアの原料となる鉄鋼は、長年の取引関係を築いた安定供給に理解のあるサプライヤーから仕入れています。全ての鉄鋼は荷受け時に100%チェックされます。
ハイテクノロジー
設備投資を継続して行い、製造設備は常にアップデートされています。多くの工程が全自動化されており、スピード製造、品質の一貫性と再現性が一層向上しています。
トレーサビリティ
先端シャフト、継手シャフトには全て刻印が押されており、ロット情報を管理するトレーサビリティとなっています。
検査体制
CHANCE社の研究所は業界でも他に類を見ません。研究所には7つの検査機械があり、定格の検証、品質保証、新製品の開発、そして新たな鉄鋼供給業者の選定に用いられます。
ヘリカルピアができるまで -Factory Tour-


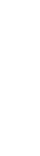





原材料の仕入れ
ヘリックスの製造に使用されるコイル状に巻かれた鋼板がセントラリア工場に運ばれます。荷降ろしされた後、品質部門が発注した仕様を満たしているか確認します。それと同時に、先端シャフトと継手シャフトの原材料となる棒鋼が鋼材倉庫から搬入されます。
パンチング
コイル状の鋼板は500トンのプレス機にかけられます。プレス機は1分間に30個の速さで鋼板を打ち抜き、ヘリックスに成形します。
鍛造成形
シャフトとなる棒鋼は鍛造加工を行うロボットアプセッターに送られます。この全自動機は4つのオーブンで、棒鋼を1260℃まで熱します。1260℃に達したら、ロボットアームはシャフトをつかみ、回転させ、ひっくり返し、片方の端部を圧縮成形する機械にセットします。適切な温度に達してないシャフトは機械によってはじかれます。
穴あけ・切断・打刻
次に、ロボットアームは穴あけと刻印を押す機械へ、シャフトを移動させます。刻印はロット情報を管理するトレーサビリティとなります。
溶接
ハイテクロボット溶接セルではスクエアシャフトとラウンドシャフトの製造が行われます。この最先端ロボットはラウンドシャフトをつかみ、シャフトを角度をつけて半分にカットし、打刻し、一度に4〜6個の穴を開け、ほんの数分でヘリックスを溶接します。
メッキ加工
メッキ加工を行うセルは1億円以上投資して改修とアップデートを経た工程です。
組立/出荷前検査
梱包の前に、組立部門が品質を確認するための最終製品チェックを行います。そして、メッキのドリップを削り取ります。これらの作業を経て、製品は物流センターに手渡されます。
梱包/出荷
物流センターでは、毎年、知識豊富で信頼できるスタッフが4万点以上の製品パッケージを荷受け、保管、出荷しています。ハンディターミナルによって効率性と正確性を継続的に向上させることを可能にしました。